11 Years Manufacturer STEEL SHAFT for Gabon Factory
Short Description:
Barrel/flange diameter up to 1.600 mm Ø Length up to 15.000 mm Weight from 10 kg to 35.000 kg
11 Years Manufacturer STEEL SHAFT for Gabon Factory Detail:
Barrel/flange diameter | up to 1.600 mm Ø |
---|---|
Length | up to 15.000 mm |
Weight | from 10 kg to 35.000 kg |
Product detail pictures:
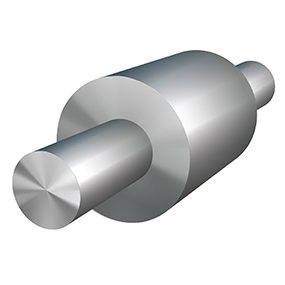
11 Years Manufacturer STEEL SHAFT for Gabon Factory, The product will supply to all over the world, such as: , , ,

