Good Quality STEEL DISC to Korea Importers
Short Description:
Diameter up to 1.200 mm (smaller dias correspondingly thicker) Thickness up to 600 mm
Good Quality STEEL DISC to Korea Importers Detail:
Diameter | up to 1.200 mm (smaller dias correspondingly thicker) |
---|---|
Thickness | up to 600 mm |
Product detail pictures:
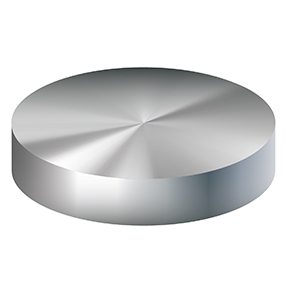
Good Quality STEEL DISC to Korea Importers, The product will supply to all over the world, such as: , , ,

