OEM Customized wholesale ROUND BAR to Israel Manufacturers
Short Description:
Length Up to 16,000 mm Diameter Max 1,200 mm
OEM Customized wholesale ROUND BAR to Israel Manufacturers Detail:
Length | Up to 16,000 mm |
---|---|
Diameter | Max 1,200 mm |
Product detail pictures:
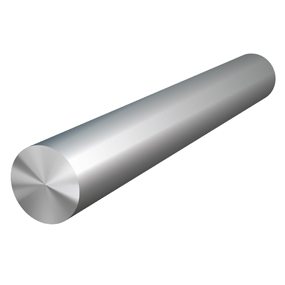
OEM Customized wholesale ROUND BAR to Israel Manufacturers, The product will supply to all over the world, such as: , , ,
Part 3
Blacksmithing for beginners shows you how to harden & temper carbon steel in the forge

