Popular Design for STEEL BLOCK to Houston Manufacturer
Short Description:
Length max. 6.000 mm Width max. 1.800 mm Thickness max. 1.000 mm (in case of smaller thickness greater length and width) Weight max. 30.000 kg
Popular Design for STEEL BLOCK to Houston Manufacturer Detail:
Length | max. 6.000 mm |
---|---|
Width | max. 1.800 mm |
Thickness | max. 1.000 mm (in case of smaller thickness greater length and width) |
Weight | max. 30.000 kg |
Product detail pictures:
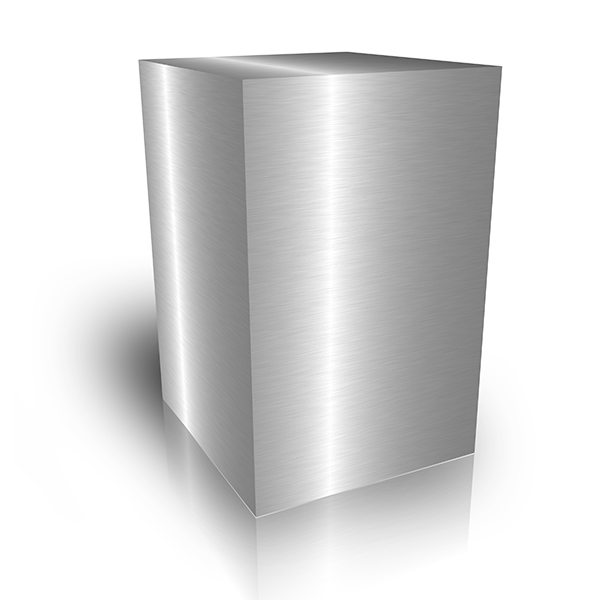
Popular Design for STEEL BLOCK to Houston Manufacturer, The product will supply to all over the world, such as: , , ,
A dowel is a solid cylindrical rod, usually made from wood, plastic, or metal.In its original manufactured form, a dowel is called a dowel rod.Dowel rods are often cut into short lengths called dowel pins.Dowels are employed in numerous, diverse applications including axles in toys, detents , structural reinforcements in cabinet making, and supports for tiered wedding cakes.
—Image-Copyright-and-Permission—
About the author(s): Ivory
License: Public domain
Author(s): Ivory (https://commons.wikimedia.org/wiki/User:Ivory)
—Image-Copyright-and-Permission—
This channel is dedicated to make Wikipedia, one of the biggest knowledge databases in the world available to people with limited vision.
Article available under a Creative Commons license
Image source in video
website:https://www.reliancemetalresource.com/
Tianjin Reliance Steel Pipe Industry & Trade Co., Ltd. was officially founded in 2004, and is located in Caigongzhuang Industrial Area in Jinghai County, Tianjin, China. We are a joint-stock enterprise, with 3 branch plants.
Our main products are:
Welded Pipes, Square & Rectangular Hollow Section Tubes
Galvanized Steel Welded Pipe and Pre-galvanized Steel Pipes.
Tel:(86) 189-2030-3008
Fax:(86) 022-23757190
E-mail:admin@reliancesteel.cn
Address:Hi-Tech information square, NanKai district of Tianjin.

