Wholesale Discount CUSTOMIZATION to Jordan Importers
Short Description:
According to the customers’ demand.
Wholesale Discount CUSTOMIZATION to Jordan Importers Detail:
According to the customers’ demand.
Product detail pictures:
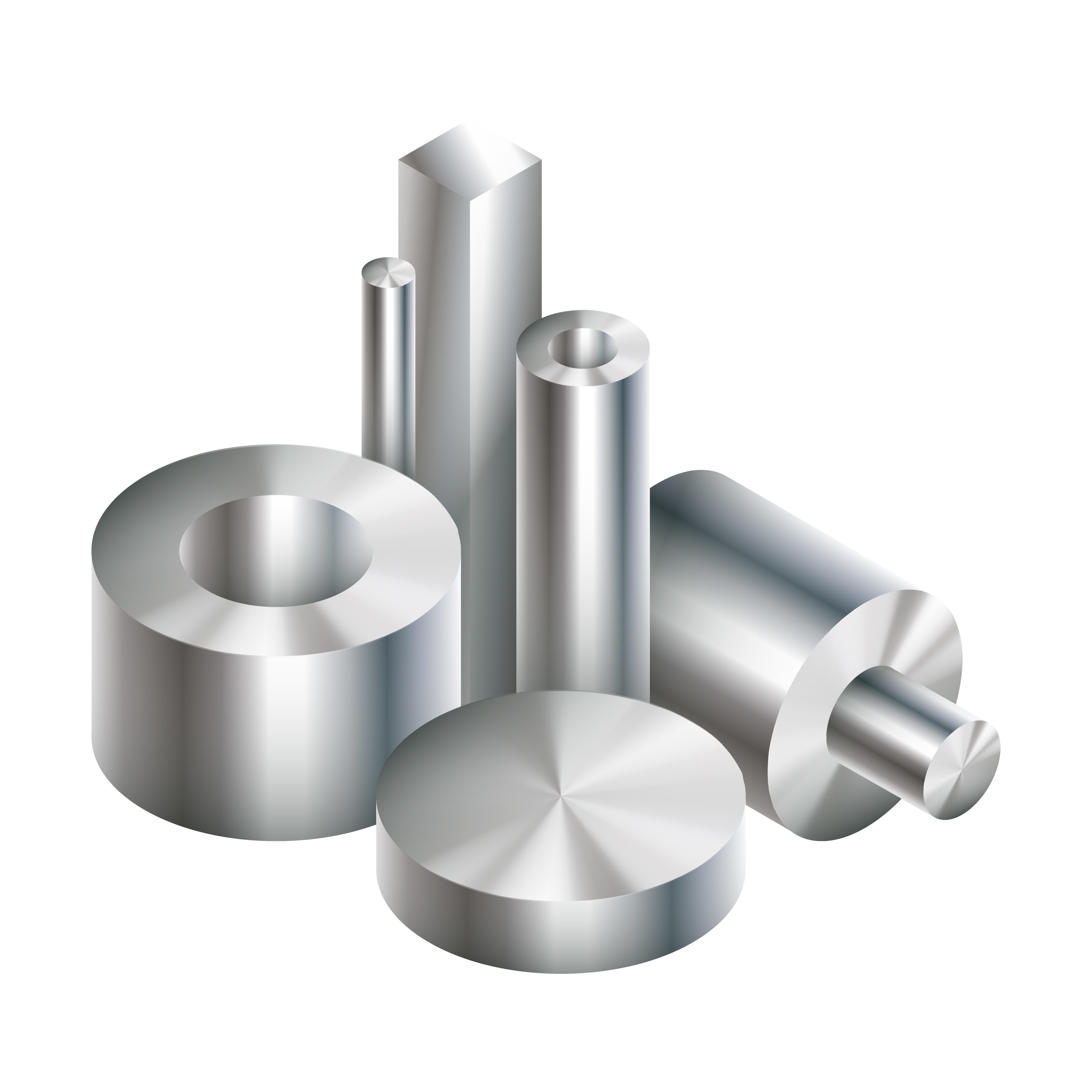
Wholesale Discount CUSTOMIZATION to Jordan Importers, The product will supply to all over the world, such as: , , ,
Điện lạnh Duy Hải là kênh chia sẻ bất chấp về kỹ thuật cho thợ sửa chữa Điện Lạnh dân dụng. Tôi sẽ hướng dẫn bạn những kinh nghiệm sửa chữa Điện Lạnh Online, Đối với những anh em mới học điện lạnh cơ bản cũng sẽ có những kinh nghiệm xương máu của tôi…
———–*———
HƯỚNG DẪN CÂN CÁP XỬ LÝ TẮC ẨM, TẮC BẨN TỦ LẠNH
———–*———
Hãy đăng ký kênh để nhận được những video mới :https://goo.gl/xbR5wt

